Autonomous Manufacturing
POLLUX leads the autonomous manufacturing industry through intelligent automation and self-optimizing systems. We drive innovative transformations in manufacturing with AI, machine learning, and digital twin technologies, providing specialized solutions that help companies gain competitive advantages in the era of smart factories and Industry 4.0.
Redefining Manufacturing Through Autonomy
Autonomous manufacturing represents a revolutionary approach to production, where systems self-optimize, self-configure, and make decisions with minimal human intervention. This advancement moves beyond traditional automation by incorporating artificial intelligence, machine learning, and advanced robotics to create truly smart factories.
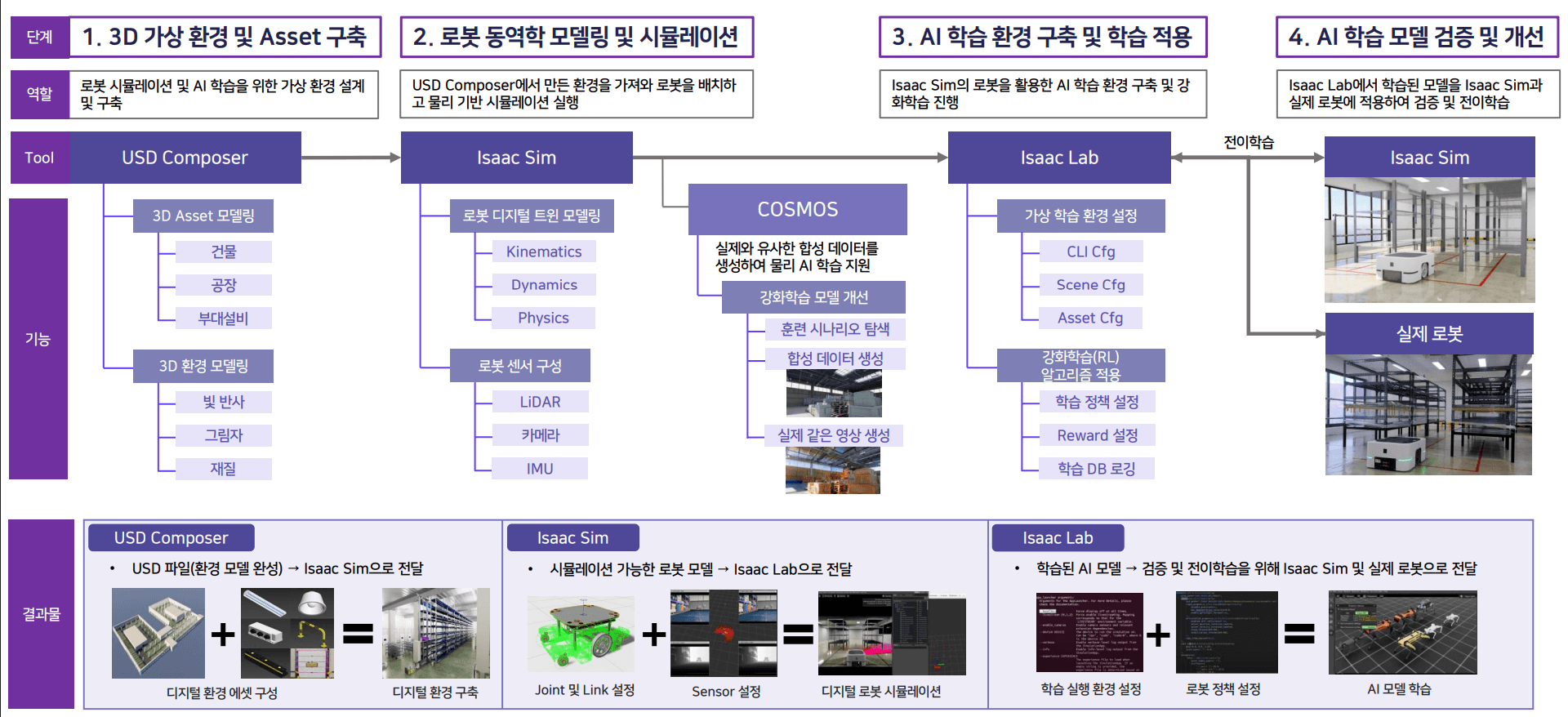
Digital Twin for Manufacturing Innovation
Fundamental Changes in 21st Century Manufacturing
Modern manufacturing is facing an unprecedented era of change. Due to global competition, diversification of customer demands, increased supply chain complexity, and accelerated technological innovation, maintaining competitiveness with traditional manufacturing methods has become challenging. In this environment, NVIDIA Omniverse-based digital twin technology offers an innovative solution for manufacturers to respond agilely to changing market conditions and secure sustainable competitive advantages.
Limitations of Traditional Manufacturing
Existing manufacturing systems rely on hardware-centered fixed production lines, facing the following limitations:
- Lack of flexibility: Significant time and cost required for physical facility reconfiguration when changing products or adjusting production volumes
- Difficulty in pre-validation: Limited methods for validating new production lines or process changes before actual implementation
- Data fragmentation: Equipment, process, and quality data are separated, making integrated analysis and decision-making difficult
- Optimization limitations: Limitations of optimization relying solely on human experience and intuition in complex production environments
The Emergence of Software Defined Factory (SDF)
NVIDIA Omniverse-based digital twin technology enables a new paradigm called Software Defined Factory (SDF). SDF accurately replicates the physical manufacturing environment in the virtual world, enabling the following innovations:
- Virtual-physical environment connection: Creating a digital replica identical to the actual factory, connecting the two worlds in real-time
- Simulation-based decision making: Validating changes in a virtual environment before actual application, reducing risks and costs
- AI-based autonomous manufacturing: Robots and equipment learn and apply optimal work methods through reinforcement learning
- Flexible reconfiguration: Enabling rapid reconfiguration and adaptation of production lines through software control
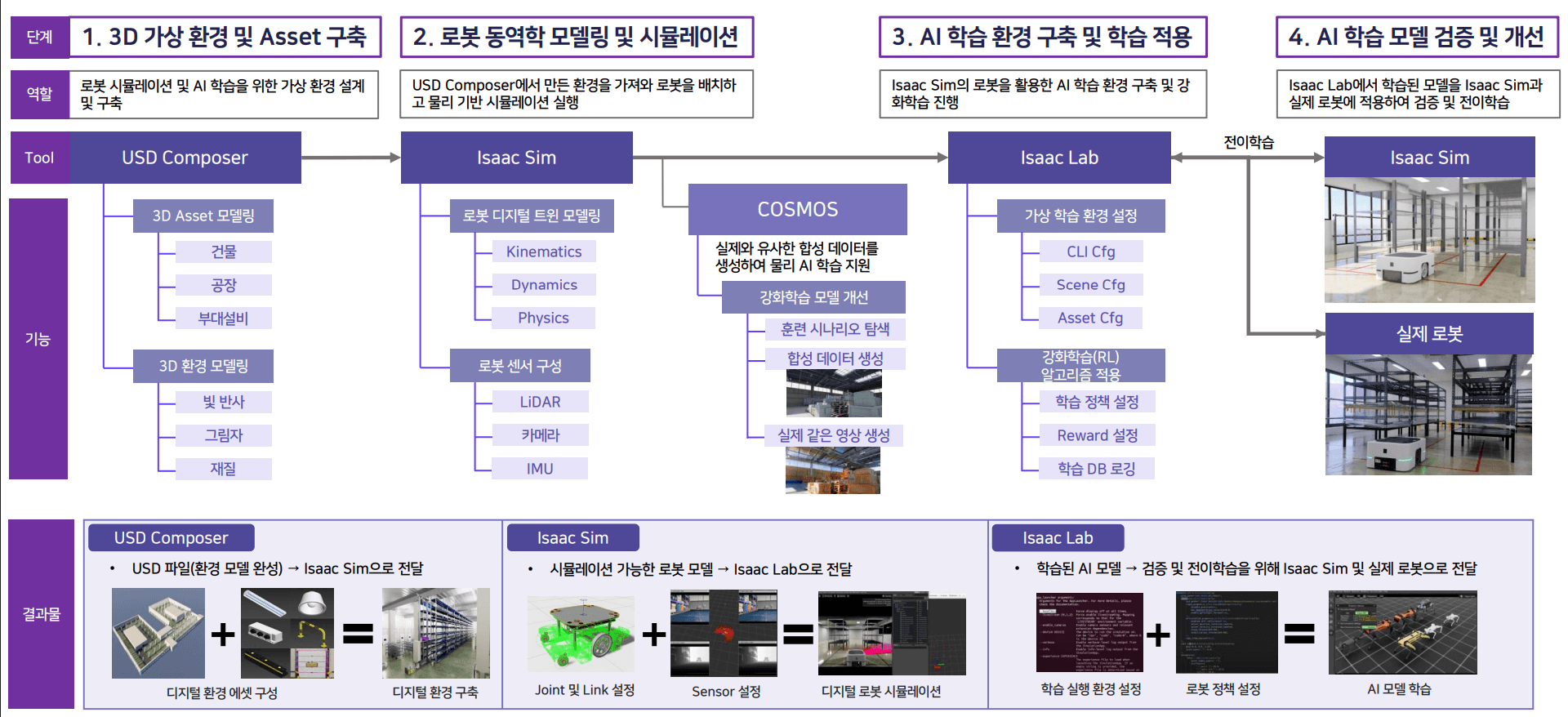
Core Values of NVIDIA Omniverse-based Digital Twin
Pollux's NVIDIA Omniverse-based digital twin service provides the following core values:
Advanced Design and Simulation
- Precise physical modeling: Minimizing differences between reality and virtual through simulations that accurately reflect actual physical laws
- Pre-validation: Validating new production lines, equipment layouts, and robot deployments in virtual environments before actual construction
- Optimal layout design: Optimizing factory layouts to reduce material movement distances and improve work efficiency
AI-based Autonomous Manufacturing Enhancement
- Application of reinforcement learning: Robots and equipment autonomously learn how to respond to various situations in virtual environments
- Large-scale parallel simulation: Discovering optimal control strategies by simultaneously simulating thousands of scenarios
- Sim-to-Real transfer: Effectively applying models learned in virtual environments to real environments
Operation Optimization and Problem Prevention
- Real-time monitoring: Reflecting actual factory data in the digital twin in real-time to understand operational status
- Predictive maintenance: Early detection of equipment anomalies for preventive maintenance
- Process optimization: Continuously optimizing production flow, resource allocation, and work sequences
Collaboration and Decision Support
- Real-time collaboration: Designers, engineers, and operators collaborate in real-time in the same virtual environment
- Data-driven decision making: Making informed decisions through analysis of various scenarios
- Education and training: Effectively conducting worker training on new equipment and processes in a virtual environment
Concrete Business Outcomes
Manufacturing companies that have adopted NVIDIA Omniverse-based digital twins can achieve the following specific outcomes:
- Reduced design and construction time: Up to 30% reduction in production line design and construction time
- Productivity improvement: 15-25% productivity increase through optimized processes and automation
- Energy efficiency improvement: Up to 20% reduction in energy consumption through optimized equipment operation
- Defect rate reduction: Up to 25% reduction in defect rates through predictive quality management
- Increased flexibility: Up to 50% reduction in production line conversion time when changing products
- Decision-making speed improvement: Up to 40% reduction in decision-making time through simulation-based decision making
Technical Implementation
Pollux's Omniverse-based digital twin solution consists of the following elements:
- USD Composer: 3D modeling and environment creation for factory buildings, equipment, robots, etc.
- Isaac Sim: Physics-based simulation of robots and equipment, sensor data simulation
- Isaac Lab: AI model learning environment for robots and autonomous systems
- Digital-physical connection technology: Bidirectional data communication between actual equipment and digital twins
- AI Ops: Verification, management, deployment, and monitoring of trained AI models
Humanoid Robot Implementation
Essential Element for Strengthening Manufacturing Competitiveness
Manufacturing is facing challenges that require constant adaptation in rapidly changing economic and technological environments. Aging populations, shortage of skilled labor, and increasing consumer demands for customized products are issues difficult to solve with traditional manufacturing methods. In this context, humanoid robots are emerging as a key element determining the future competitiveness of manufacturing.
Changing Environment and the Need for Humanoid Robots
Responding to Economic Environmental Changes
- Solving labor shortage issues: In many developed countries, the manufacturing workforce is aging, and younger generations tend to avoid manufacturing jobs. Humanoid robots can fill this labor gap.
- Production cost optimization: In the long term, despite high initial investment costs, humanoid robots can alleviate pressures from rising labor costs and increasing welfare expenses.
- Implementing 24-hour production systems: Humanoid robots can work continuously without fatigue or loss of concentration, greatly improving productivity.
Responding to Technical Environmental Changes
- Flexible production systems: Modern consumers want customized products, which requires frequent reconfiguration of production lines. Humanoid robots can quickly adapt to various tasks through programming.
- Quality consistency assurance: Unlike humans, humanoid robots perform tasks with consistent precision, minimizing product quality variability.
- Data-driven decision making: Sensors embedded in robots collect various data from the production process, enabling real-time analysis and optimization.
Enhancing Future Competitiveness
- Integration with smart factories: Humanoid robots can become central elements of fully automated smart factories when combined with technologies like IoT, AI, and big data.
- Improving sustainability: Energy-efficient operations and minimal resource waste enable environmentally friendly production methods.
- Replacing hazardous work environments: Humanoid robots can substitute for humans in dangerous work environments, improving workplace safety.
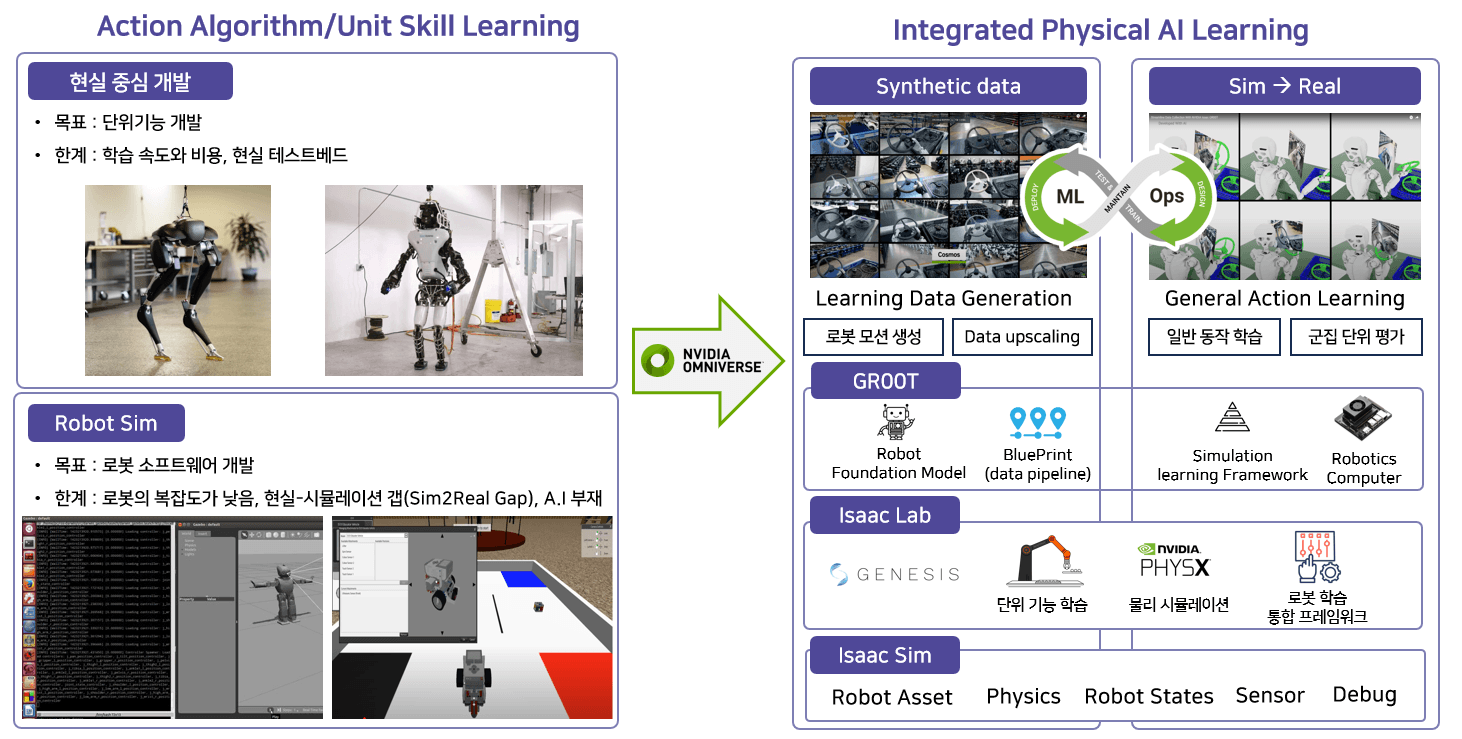
Preparation for Humanoid Robot Implementation in Manufacturing Companies
Risk Minimization through Digital Twins
- Building virtual simulation environments: Create virtual replicas of actual production environments using digital twin technology, simulating various scenarios before implementing humanoid robots.
- Pre-validation and optimization: Pre-validate and optimize robot movements, work sequences, and production line layouts in virtual environments to identify and resolve potential issues before actual implementation.
- Real-time monitoring and predictive maintenance: Link actual robots with digital twins to monitor performance in real-time and perform proactive maintenance by predicting potential issues.
- Worker education and training: Workers can safely learn and train collaboration methods with humanoid robots in digital twin environments.
- Gradual expansion strategy: Introduce humanoid robots gradually, starting with processes validated through digital twins, to distribute risks.
Technical Preparation
- Infrastructure construction: Build network infrastructure and cloud systems for robots to operate smoothly.
- Integrated system design: Design architectures to effectively integrate existing production systems with humanoid robots.
- Strengthening cybersecurity: Connected robot systems can be vulnerable to cyber attacks, requiring robust security frameworks.
- Digital twin construction: Pre-simulation through digital twins and reinforcement learning in the field are necessary to eliminate various risk factors and strengthen the field adaptability of humanoids.
- Sensor network construction: High-precision sensor networks are needed for accurate synchronization between digital twins and actual environments.
Strategic Decision for Sustainable Growth
Strategic Preparation for Humanoid Implementation
Implementing humanoid robots is a strategic decision that fundamentally changes the manufacturing paradigm. Pre-validation and risk minimization strategies using digital twin technology make this transition safer and more effective. To maintain and strengthen competitiveness in a rapidly changing environment, manufacturing companies should begin preparing for digital twin-based humanoid robot implementation now. Along with thorough preparation in technical, organizational, financial, and ethical aspects, risk management strategies through digital twins will be a key element for successful humanoid robot implementation.
Key Features
Self-Optimization
Systems that continuously analyze performance data and adjust parameters to maximize efficiency, quality, and throughput.
Predictive Intelligence
AI-driven prediction of machine failures, maintenance requirements, and production bottlenecks before they impact operations.
Adaptive Manufacturing
Production lines that can reconfigure themselves to accommodate different products with minimal downtime.
Decentralized Decision-Making
Distributed intelligence where individual machines and systems can make localized decisions within a broader production framework.
Challenges in Traditional Manufacturing
Traditional manufacturing faces significant constraints, including inflexible production lines, reactive maintenance practices, dependency on manual intervention, and difficulty adapting to changing market demands. These limitations lead to inefficiencies, increased downtime, inconsistent quality, and higher operational costs.
Limited Adaptability
Rigid production systems that struggle to accommodate product variations or volume changes.
Maintenance Inefficiencies
Reactive approaches to equipment maintenance that lead to unexpected downtime and production losses.
Human Dependency
Over-reliance on human decision-making for process optimization and problem resolution.
Data Utilization Gaps
Inability to effectively collect, analyze, and leverage operational data for continuous improvement.
Transformative Solutions
Autonomous manufacturing provides comprehensive solutions that address traditional production constraints while creating new opportunities for efficiency, quality, and innovation.
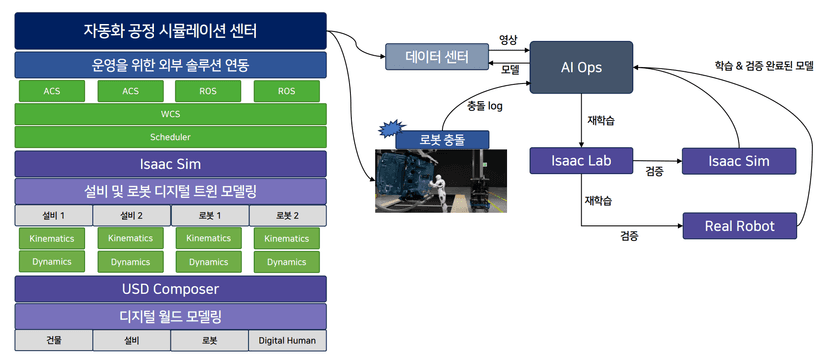
Smart Manufacturing Systems
Integration of IoT sensors, edge computing, and cloud platforms that enable real-time monitoring and control of production processes across the entire factory floor.
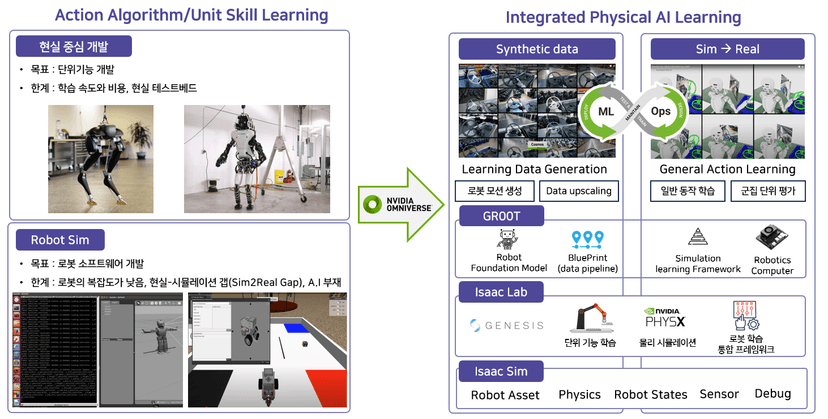
Advanced Robotics and Automation
Collaborative robots and automated guided vehicles that work alongside humans, handling repetitive, dangerous, or precision tasks while adapting to changing production requirements.

Industrial IoT Networks
Comprehensive sensor networks and data analytics platforms that gather and process vast amounts of operational data, enabling predictive maintenance, quality assurance, and process optimization.
Business Benefits
Operational Excellence
30-50% reduction in production downtime through predictive maintenance and self-healing systems.
Enhanced Flexibility
Ability to adapt to new products or volume changes up to 75% faster than traditional manufacturing setups.
Quality Improvements
Defect reduction of 15-30% through continuous quality monitoring and autonomous correction.
Resource Optimization
Energy consumption reductions of up to 20% through intelligent resource management and optimized processes.
Competitive Advantage
Faster time-to-market for new products and ability to offer mass customization without significant cost increases.
The Future of Manufacturing
Autonomous manufacturing represents not just an incremental improvement, but a fundamental reimagining of how products are made. By embracing these technologies and approaches, manufacturers can create resilient, responsive, and highly efficient operations that meet the demands of today's dynamic global marketplace while positioning themselves for continued success in the future.